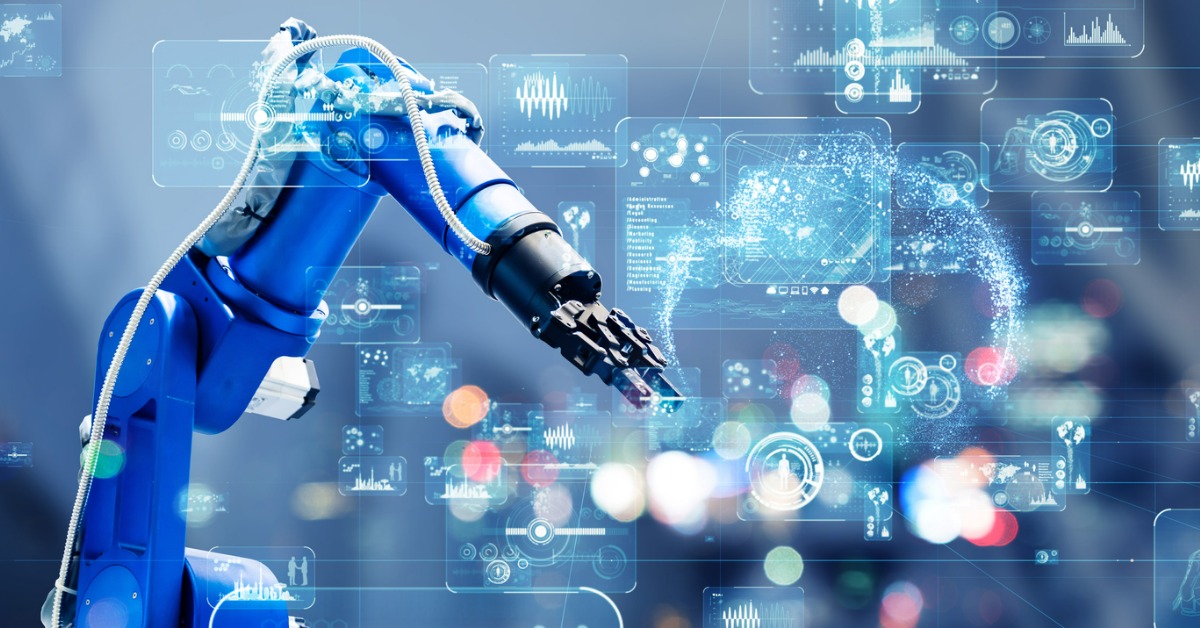
Cloud Manufacturing and its role in the 4th Industrial Revolution
In every industry, analysts and marketers are forever declaring that this or that innovation marks the beginning of a new era, an epochal moment that will forever separate the past from the future.
Sometimes it does—fire, the wheel, transistors, iPhones. But more often, it’s an incremental change that might be seen in retrospect as one of several concurrent innovations that together constituted an important inflection point.
Industry 4.0
Depending on who you ask, we are either undergoing the fourth industrial revolution (or 4IR for short) or we are undergoing the fourth phase of The Industrial Revolution. Fortunately, it doesn’t matter which, except to some historians. For convenience, we will number our industrial eras as though they were software versions—even though no upgrade to Industry 4.1 is likely:
Industry 1.0, in the 18th century, is what we commonly think of as the industrial revolution. It was driven by the harnessing of water and steam power and large-scale mechanization of industrial processes.
Industry 2.0, in the 19th century, saw the electrification of industry, along with the development of mass production and assembly-line capabilities.
Industry 3.0, in the 20th century, leveraged advances in computerization, automation, and electronics integrated throughout industrial production facilities.
Industry 4.0 is where we are now. Smart cyber-physical systems are emerging quickly, the network is everywhere, and the Internet of Things connects industrial infrastructures to each other and to the cloud. And rapid, AI-powered data collection and analysis is enabling greater business agility and automation.
Cloud manufacturing
According to a 2022 essay in NIST’s Marketing Innovations blog, it’s useful—especially when considering manufacturing through the lens of cybersecurity—to think of Industry 4.0 as the confluence of four different but overlapping innovations:
Cyber-physical systems (CPS) and Cobots
Internet of Things (IoT) and big data
Cloud manufacturing
Automation
All of these innovations rely on—and are driven by—the ability to collect, analyze, share, and act on information in real-time. Industrial machinery is interconnected with production management systems; multiple manufacturing processes share information transparently; and information is gathered, shared, and used throughout the manufacturing lifecycle.
Cloud manufacturing, in particular, introduces the concept of a “manufacturing cloud.” This refers to the transformation of certain resources and capabilities into cloud-delivered services. In effect, it is the virtualization of those resources and capabilities.
Cyber systems are able to collect information, analyze it, make decisions based on it, and act independently to implement those decisions via their interconnection with physical industrial systems. Of course, human operators and users remain in the loop, sharing the ability to monitor decisions and execute control over physical systems. However, to optimize efficiency and agility, cyber systems are granted increasing levels of independence in how they control physical systems.
Security and cloud manufacturing
If you’re a cybersecurity professional, that last paragraph probably made you at least a little nervous.
As well it should. There are both cultural and technical reasons to be concerned about new cybersecurity vulnerabilities that may emerge with the adoption of cloud manufacturing.
Safety over security
On the cultural side, there’s the fact that manufacturing traditionally is concerned most of all with safety—that is, the safety of human operators interacting with industrial machinery. That concern for safety is far ahead of concern for security among designers and managers of industrial manufacturing systems.
Again, traditionally, operational technology (OT)—even up to Industry 3.0 and the introduction of computerization and automation—has been effectively air-gapped from information technology (IT), meaning that there have been few reasons to be concerned about information security.
OT-IT integration
Now, however (and here we’re getting into the technical side), Industry 4.0 and cloud manufacturing are pretty much defined by the integration of OT and IT. Which means that criminals who penetrate IT infrastructures can also move laterally into industrial systems, potentially causing massive real-world damage by sabotaging machinery. Likewise, hacking into a car-building robot no longer only lets you mess up the assembly line. It now serves as a vector into your target’s entire IT infrastructure. These threats constitute an entirely novel form of cyber risk for administrators used to designing industrial systems with safety as their top concern.
Slow turnover
Yet another area of risk comes from the fact that industrial machinery typically depreciates over decades, and therefore is very rarely replaced or updated. And yet, the speed with which cybercriminals develop new strategies and technologies demands constant updating in order to maintain adequate security over time.
Securing Cloud Manufacturing
Adjusting mindsets and cultures to put security front and center has to be an organization-wide initiative that starts with consultation and buy-in from managers in both the IT and OT silos—with the aim of eliminating the silo mentality. It may well require some reorganization and the establishment of new roles.
On the technical side, much can be achieved by the implementation of a modern network security platform that is specifically designed to address IoT and IIoT concerns by fully integrating IT and OT security and bridging on-premises and cloud-based resources and capabilities. Barracuda Network Protection includes features and capabilities designed for industrial security use cases, implementing best practices to extend advanced security across interconnected OT and IT surfaces.
Subscribe to the Barracuda Blog.
Sign up to receive threat spotlights, industry commentary, and more.